ICCS Catalyst Characterization
Comprehensive Catalyst Characterization
- A high precision, highly sensitive thermal conductivity detector (TCD) to monitor changes in the concentration of gases flowing into and out of the reactor.
- An internal cold trap with Peltier system for accurate temperature control across the range -20 to 65oC for the removal of condensable fluids (e.g. water produced during reduction of oxides)
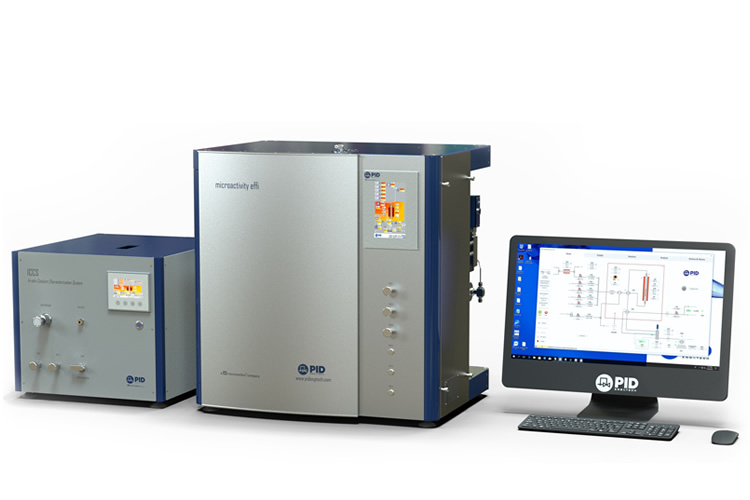
Comprehensive Catalyst Characterization
The Micromeritics in-situ Catalyst Characterization System (ICCS) is an advanced catalyst characterization tool that allows the user to study the impact of a reaction on critical parameters such as number of active sites, under precisely controlled, process-representative conditions.
A standalone accessory designed to complement any dynamic laboratory reactor system, such as the MicroActivitySystems, the ICCS adds two new capabilities: Temperature Programmed Analyses (TPx) and Pulse Chemisorption.
These well-known and time-tested techniques may now be performed on a fresh catalyst and then repeated on a used catalyst without removing the material from the reactor. This enables a detailed comparison of the catalyst, notably the number of active sites, before and after use. Users benefit from obtaining both temperature programmed analyses and pulse chemisorption data for the same aliquot of sample used for reaction studies. Performing these analyses in-situ virtually eliminates the possibility of contamination from atmospheric gases and moisture which may damage the active catalyst and compromise data integrity.
The ICCS incorporates:
- A high precision, highly sensitive thermal conductivity detector (TCD) to monitor changes in the concentration of gases flowing into and out of the reactor.
- An internal cold trap with Peltier system for accurate temperature control across the range -20 to 65oC for the removal of condensable fluids (e.g. water produced during reduction of oxides)
- Two mass flow controllers for precise gas control (pressure control is via the reactor system).
- An interactive reporting and control system with a versatile and intuitive graphic user interface for streamlined command sequencing, experimental design and results analysis.
To enable:
- The safe, efficient and comprehensive characterization of samples under process-representative conditions, up to a maximum pressure of 20 bar.
- The application of a wide variety of tests including pulse chemisorption, temperature programmed reduction (TPR), desorption (TPD) and oxidation (TPO), and physisorption (optional).
- Multiple characterizations of the same catalyst sample, following reaction or regeneration to investigate reaction, deactivation and regeneration mechanisms.
Specifications
Electrical
Voltage | 240 VAC 10 A, single phase |
Frequency | 50 – 60 Hz |
Power | 10 A, single phase |
Control Module: Minimum Requirements
Processor | Intel Core I3 or equivalent |
Operating Systems | Windows 7/8/10 (32/64 bits |
RAM | 4 GB |
Hard Drive | 500 GB |
Temperature System
Valve Box | Up to 180 ºC |
Heated Line | Up to 180 ºC |
Cold Trap | By a Peltier system from -15 ºC up to 70 ºC |
Pressure System
Operating Pressure | Up to 20 bar(g) max. |
Options
Loop Volume | 0.5 cc and 1.0 cc |
Gas Flow Rate
Number of Mass Flow Controller | 2 |
Max. Required Inlet Pressure | 30 bar |
Flow Range | MFC1 Range 1: 0 – 800 mlN/min Range 2: 800 – 3000 mlN/minMFC2 Range: 0 – 150 mlN/min |
Gas Delivery
Requirements | Pressure of 30 bar and vent connections with 1/8’’ connection. Connectors to cylinders are not included and to be provided by the customer |
Physical
Height | 445 mm (17.52 ”) |
Width | 545 mm (21.46 ”) |
Length | 500 mm (19.69 ”) (without computer) |
Weight | 40 kg (88.2 lbs.) |
Environment
Temperature | 10 – 35 ºC operating |
Humidity | 10 – 60 % without condensation |
Recommendation | Avoid direct sunlight, and direct cool or hot sources |
Principle of Operation
The typical operation of the ICCS begins with loading of the catalyst into the reactor system. The catalyst may then be characterized by the temperature programmed methods; temperature programmed reduction (TPR) is commonly used for supported metal catalysts while temperature programmed desorption (TPD) may be the best choice for acidic or basic catalysts. The TPx is often followed by pulse chemisorption to determine the number of active sites. This use of TPx and pulse titration provides a description of the fresh (unused) catalyst under representative conditions (notably at elevated pressure).
After performing this initial characterization, a user may then proceed with reaction studies on the exact same sample without adding any additional catalyst or transporting the catalyst to a different device.
Upon deactivation or simply after a prolonged period of testing, the used catalyst may then be analyzed in the same way as the fresh material employing TPx and pulse chemisorption under identical conditions. This strategy provides a method for comparing the key characteristics of the catalyst such as number of active sites before and after use without removing the catalyst from the reactor.